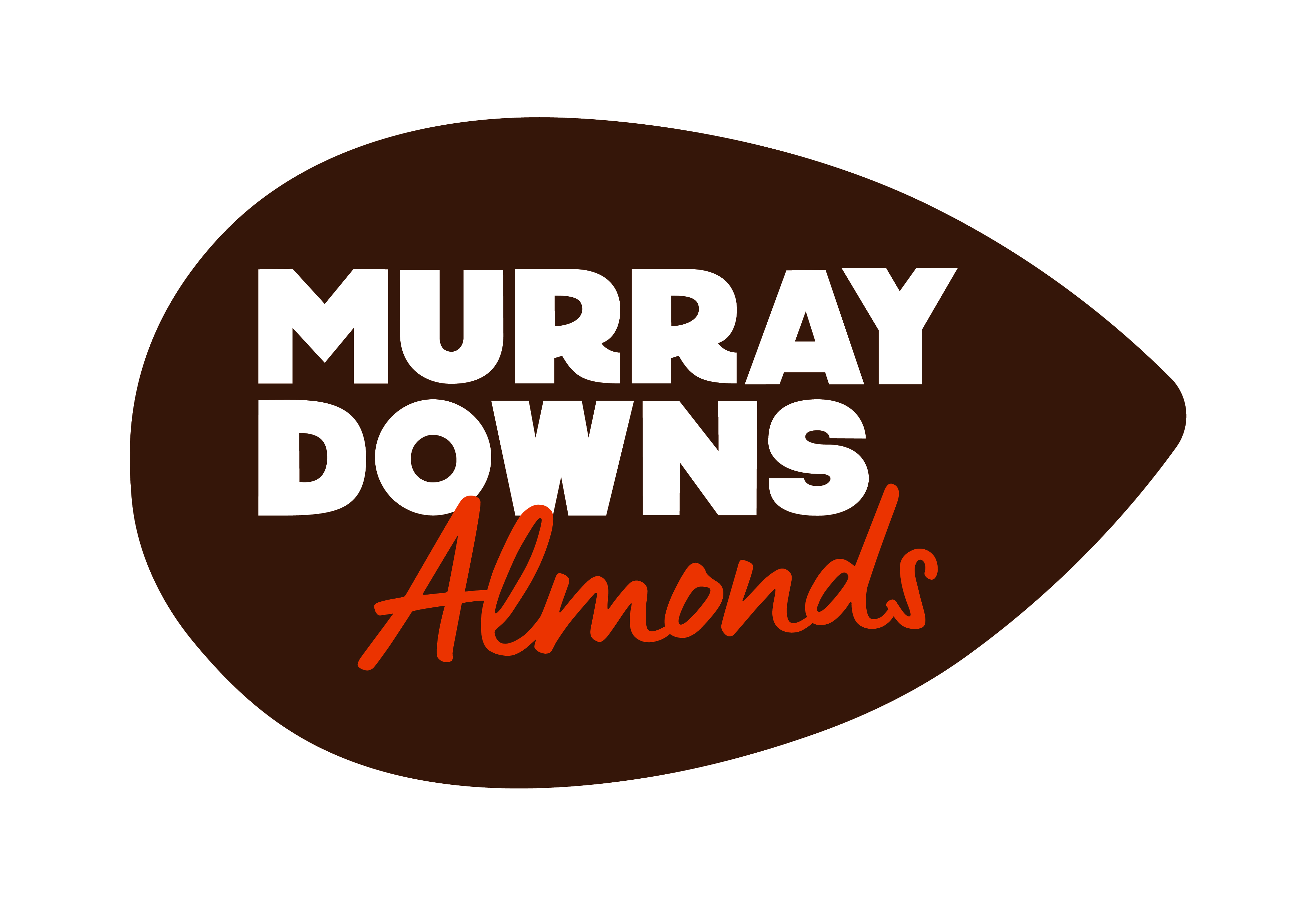
Murray Downs Processing (Aus Farming), NSW
Food Processors
ALMADS
Murray Downs Processing (Aus Farming) is a growing company that have expanded from farming their own Almond crops, to now taking on the endeavour to process their own product in 2024.
The new Almond Huller / Sheller / Processor and Packer is being constructed in regional New South Wales, Murray Downs area, Australia.
Murray Downs Processing have committed to take the full suite of ALMADS Modules from Grower Receiving through to Customer Packed Orders, Shipping and Invoicing and everything in between.
Our goal is to take their brand new almond huller, sheller, processor, and packer operations paperless, using #ALMADS and RFID technology, from the orchard to the final packing stage. We’re always on the lookout for cutting-edge solutions, and this project is no different. This will be a groundbreaking first and we are excited to partner with them.

Waliz Nuts, Newrybar NSW
Food Processors
ALMADS
Another Australian Macadamia Processor joins our ALMADS Family this year.
Waliz Nuts, located in the picturesque town of Newrybar, not far from the beaches of Byron Bay, New South Wales.
Starting with their first phase ALMADS implementation concentrating on Grower Receiving, Quality Assurance and Grower Payments, we will then move onto cracking, sorting and packing.
Waliz Nuts is a progressive, expanding company and we are excited to be along for the ride with them and assist them with efficiency and information.
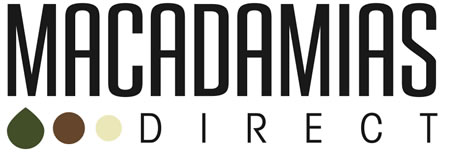
Macadamias Direct, Ballina NSW
Food Processors
ALMADS
Over the past 12 months we have been busy redeveloping our flagship ALMADS system to become more of a configurable multi-commodity system so that it can be potentially used for any tree nut processing.
This has come into play recently with the signing of a new Macadamia cracking and processing client in Country NSW.
Regional IT formally welcome Macadamias Direct to our ALMADS family. We look forward to working with you with this upcoming 2022 season.
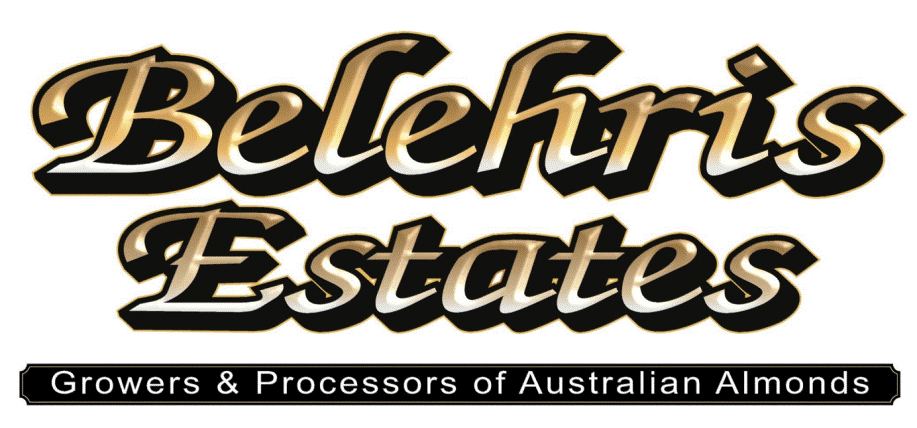
Belehris Estates, Renmark SA
Food Processors
ALMADS
ALMADS scalability is on full display with the signing and new installation of ALMADS into one of the more smaller almond processing and packing clients.
We welcome Belehris Estates and we wish you luck with current season. We had to work with extremely short lead times from when we were contacted to when we had to deliver our software. Although time lines were tight, we managed to install the first phase of the project in a week ready for the first packing work order.
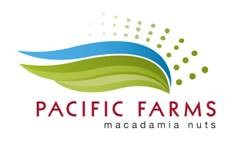
Pacific Farms, Brooklet NSW
Food Processors
Supply Chain System – We have recently been involved in Pacific Farms expansion to Zimbabwe and look to support their supply chain system for this coming harvest in all countries.
Tainted as a future ALMADS Macadamia client, Pacific Farms will evolve over time to join the many processors and commodities ALMADS now supports.
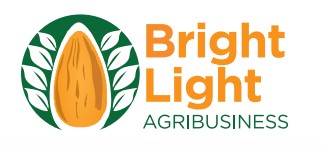
Bright Light Agribusiness, Hattah VIC
Almond Huller / Sheller/ Processor
ALMADS
Bright Light Agribusiness (BLA) is a new Almond Huller / Sheller / Processor being constructed in regional Victoria, Australia.
BLA have committed to take the full suite of ALMADS Modules from Grower Receiving through to Customer Packed Orders, Shipping and Invoicing and everything in between.
ALMADS will also be fully linked to the PLC system to reduce manual entry and alleviate human error.
We are excited to commence this project and look forward to their first harvest in 2021.
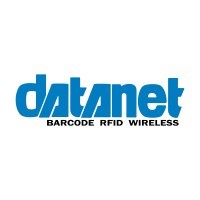
Datanet, Adelaide SA
Hardware Solutions
Datanet have worked with Regional IT on many projects supplying and advising ALMADS clients on industrial hardware and technologies to seamlessly interface with ALMADS in recent years.
In a case of role reversal, Datanet have engaged us in a project that puts our best skills to work and help them with a proof of concept.
More to come on this one.
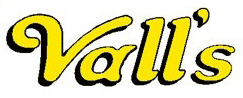
Vall’s Styrene, Berri SA, Adelaide SA and Orange NSW
Manufacturing ICS – (Invoicing System) that interfaces directly into MYOB Accounting system. This system is used to generate invoices for products sold and send a summarized form of the invoices to MYOB. Customer specific pricing on products listed on invoices can be configured in ICS allowing many differing rates that may be negotiated to be stored and seamlessly applied to an invoice once configured.
Recently Valls opted to have Regional IT develop a new small manufacturing system for the styrene operations in Monash, which runs a web system on tablets in the processing plant and interfaces directly with the new cloud based version of MYOB.
The system has now been delivered and Fred and the team are very pleased with the results!
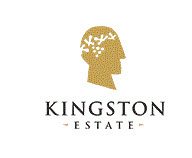
Kingston Estate Wines, Kingston on Murray, SA
Winery
LIMS (Lab Information Management System) – KEW signed with us in January 2019 and engaged us to develop a Lab Information Managements System. This system receives requests from the Wine manufacturing system and registers samples and the tests required for the sample. The results for each test are recorded and content entered is strictly monitored by configurable result rules. Once all tests are recorded, they are sent back to the wine manufacturing system. The samples, tests and completed results also contribute towards a sample matrix which provides winemakers and management a tool to discover trends for future blends. The LIMS system also directly interfaces with some of the lab equipment to reduce keying errors, prints barcoded sample labels, provide emailing and email rules for test status along with an easy to use configurable user experience.
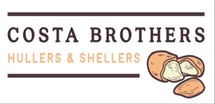
Costa Brothers, Swan Reach SA
Almond Huller/Sheller
ALMADS
Regional IT is excited to welcome Costa Brothers Hullers and Shellers who came on board early 2017. We have pulled all our resources together to deliver the 1st phase of an ALMADS project within 3 weeks of acceptance.
Costa Brothers have built a new plant located just our of Swan Reach, South Australia and approached us late in the project to supply software.
Phase 1 saw us deliver an Hulling and Shelling system from Grower Receivables through to Bin Shipping to Handlers. We delivered this first phase a week before the first truck arrived!
Phase 2 will see us deliver Sorting and Packing modules as well as Quality assurance, warehousing and finished good shipping.
This phase is expected to be delivered by the end of March 2017.
Therefore delivering the full project in just under 2 months!
We wish Costa Brothers well for this coming harvest and we look forward to working with you!

Nut Producers Australia/Riverland Almonds, Loxton SA
Almond Processor
ALMADS
Starting in season 2014, ALMADS was developed to cater for Riverland Almond’s sorting, packing and retail packing operations. ALMADS is also interfacing with SAP that will now only serve as just an ordering and financial system. ALMADS replaces all inventory and processing operations because it is being developed to suit almond processing specifically.
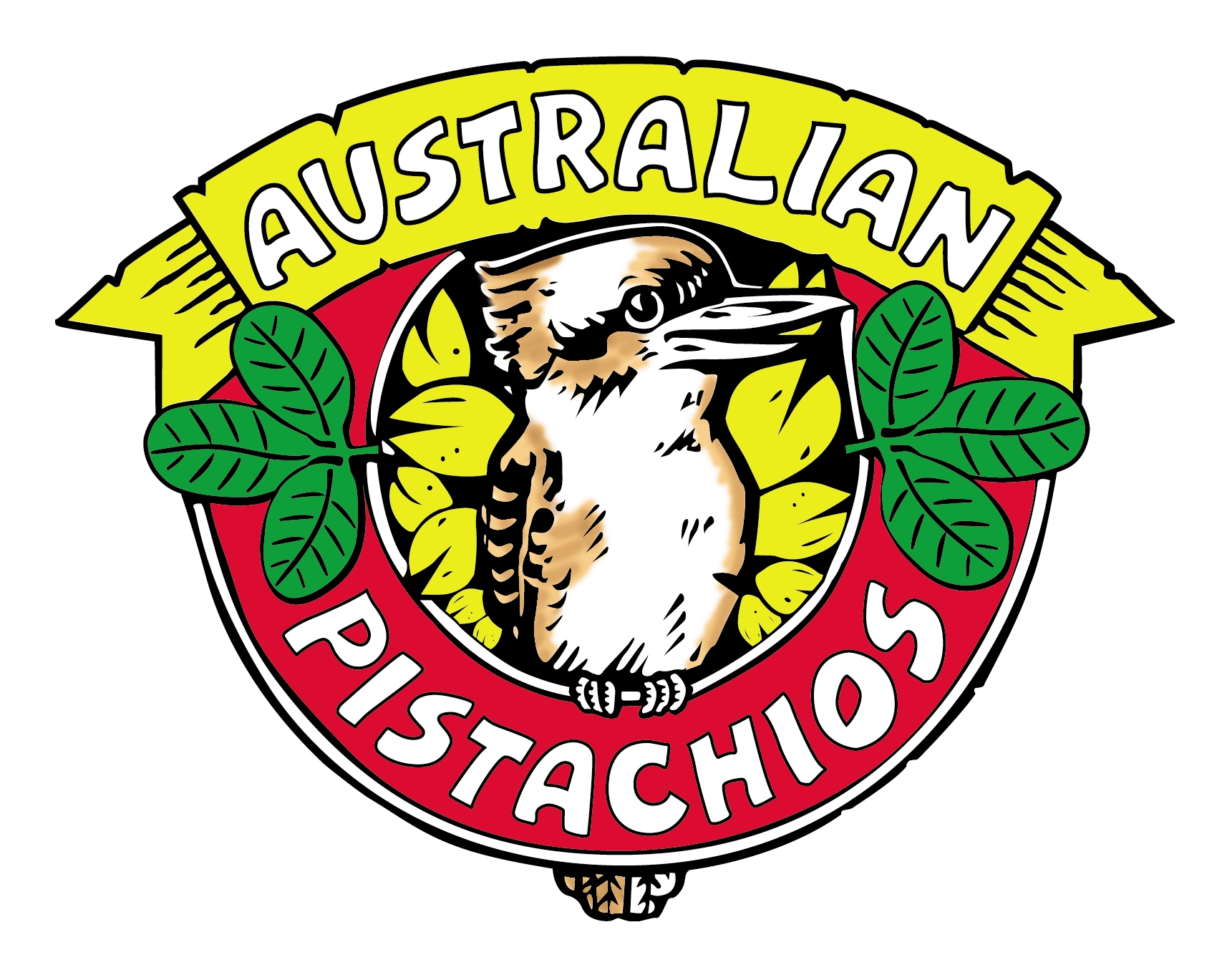
Australian Pioneer Pistachio Co, Robinvale VIC
Pistachio Processing
ALMADS
Since 2016 season, ALMADS has been adapted to suit the pistachio commodity using the Receiving, Hulling, Marketing, QA, Grading & Picking, Sorting & Packing, Shipping and Reporting modules all whilst interfacing with SAP.
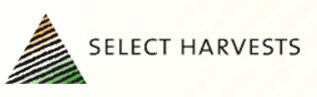
Select Harvests Limited, Wemen VIC
Huller/Food Processor
ALMADS – One of the largest huller / processors in Australia, Select Harvests Limited signed with Regional IT in late 2010 to have an ALMADS solution developed ready for their 2011 season. All of the hulling and shelling modules were delivered prior to the season. Warehousing, Expanded QA, Inshell Finish Goods tracking, Grading and Dispatch were all developed soon after the season commenced. Season 2012 saw the delivery of the Marketing, Sorting and Packing, Micro testing, Expanded QA and Finished Goods Dispatch delivered prior to the season commenced with Reject Finished Goods and Consumable Inventory monitoring later developed. We have added more new features for season 2014 including installing the Commodity Lite module and providing ability to have linked bins both through Hulling & Shelling and Processing along with more Quality Assurance measures.
Season 2017 saw Regional IT interfacing with JD Edwards. We also now expanded ALMADS to include the use of 2D barcodes which Select Harvests will be using for the first time.
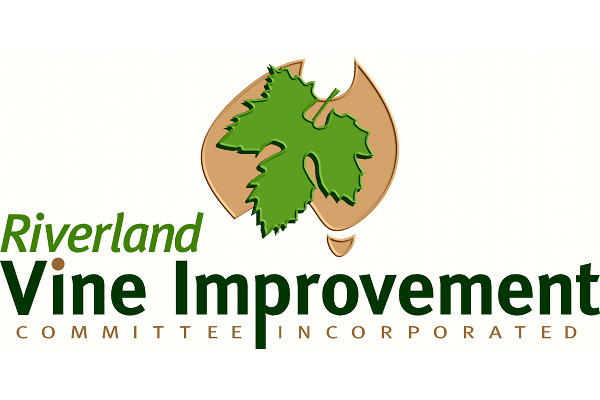
Riverland Vine Improvement Committee, Monash SA
Vine material
GERM PLASM REGISTER – In 2015 & 2016 we were pleased to be able to assist the Riverland Vine Improvement Committee developing a solution to store all pertinent information relating to vine varieties, creating a Germ Plasm Register.
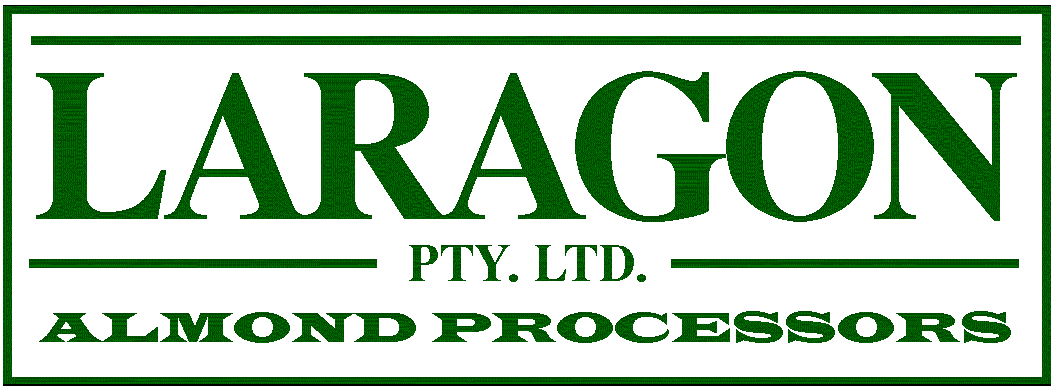
Laragon Almond Processors, Lindsay Point SA
Food Processor
LAMADS (Laragon Almond Management and Distribution System) – At Regional IT we developed a system to capture bin weights after almonds have been hulled and cracked using industrial terminals with Winsock and telnet technologies and communicating with scales and creation of barcoded technology to trace product anywhere within the sytem. Quality is captured from samples. Reports then generated for grower deliveries and quality.
2010 Season 7 with Laragon – we converted their system over to fall in line with all ALMADS versions that had since been developed for a broader market. 2011 season saw 7 new bin scales installed under each sizer chute with technology attached to each bin scale to obtain weights and provide a sizer terminal to print bin tags for each scale through the LAMADS system.
Laragon’s system has been enhanced over the past couple of seasons with the introduction of a Grower Web Portal and now sending dispatch information direct to Processors for ease of data entry.
Regional IT’s oldest Almond client are still thinking of new ways to enhance their processes and for season 2017 had Regional IT adapt their LAMADS system to communicate with their new touch screen tablets and they are now in full swing of harvest.
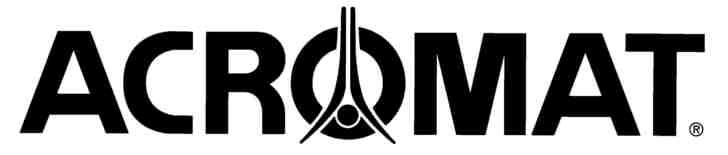
Acromat Pty Ltd, Adelaide SA
Manufacturing
Regional IT supports 4 different systems at Acromat, 3 of which were developed by Regional IT.
Manufacturing System – Enhancing & maintaining a manufacturing system that manages the production of Gym Equipment and Stadium Seating throughout the country and the world.
Payroll System (PayrollIT) – Developed a payroll system that interfaces into Acromat’s Manufacturing System and uses the operations performed by their staff as the time worked for a week.
Contracting System (ContractIT) – Developed a Contracting system that books and monitors Acromat’s Contractors’ jobs around the country. Each Contractor has a ‘lite’ version of the Contractor system installed on their computers and this version links back over the internet to a central Contractors system located on Acromat’s server. The data is live at both ends and has turned out to be an excellent management tool.
Document Archiving System (ArchiveIT) – Developed a system which stores client’s project documents electronically (most .pdf documents). The system arranges these documents and provides an easy method to search and recall any document linked to the project and client linked with the manufacturing system.

Biological Services, Loxton SA
Pest Control for Horticultural crops
‘Bio Serv’ was developed for Biological Services to track customer orders, packaging, distribution and invoicing needs.

Electrolux Home Products Australia
Manufacturing
GSQA (Global Supplier Quality Assurance System) – Created a windows based management reporting system that provides National and International Purchasing management with information about supplier performance. This system provides reports and graphs relating to suppliers scores based on early, late, under supplied or over supplied deliveries. GSQA does this by interfacing with Electrolux’s existing in house manufacturing and quality systems.
GSQA has been installed and used throughout all manufacturing divisions in Australia.
QARS (Quality Audit and Rework System) – Created a Quality Assurance system that captures the information found as a result of a Quality Audit or Reworks that are performed on finished goods. It also captures information relating to parts and part assembly quality. This information is then reported on and graphed and is presented to management as a core Key Process Indicator (KPI) for each manufacturing division in Australia and New Zealand.

Hentschke Transport, Loxton SA
Transport
TransIT – (Stand Alone Consignment Note and Invoicing System) TransIT interfaces directly into their MYOB Accounting system. TransIT has hundreds of con notes entered into it daily. Customer specific pricing and location specific pricing can easily be assigned and configured onto con notes allowing many differing rates and prices for a single item.

Berri Barmera Council, Berri SA
Government
Developed a system that interfaces with the Council’s ERP system to generate barcoded rate notices that are distributed to all rate payers of the council. The rate notice data is saved to allow historical rate notices to be reproduced. The developed system is also configurable to allow data to be dynamically changed each quarter if required.
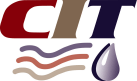
Central Irrigation Trust, Barmera SA
Water Management
Weather Station Web Graphing – Enhanced CIT’s website by including dynamic Weather Station graphing. Data was obtained from a propriety software package that dials into each weather station and downloads the specifics required. The data is then transferred and manipulated into a database. The graphs are then dynamically drawn and presented to the end user based on the criteria they have selected (i.e. moisture, rainfall, humidity and temperature over a time span).
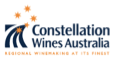
Constellation Wines (previously Hardys), Glossop SA
Wine Makers
BELIM (Lab Information Management System) – Created a system that tracks wine samples that are tested in the Berri Estates main lab. BELIM interfaces with the AS400 system using OLE to extract data about a sample and the tests that are to be performed. The tests are also registered in BELIM and the results are recorded by either user entry or direct interface with the testing instrumentation (either by serial connection or file transfer). Test results are then sent to the AS400 through OLE interface at a polling interval. Calibration, servicing and maintenance logs are also kept in BELIM. The test station technician can then be aware of any action due on the instrumentation by warnings that appear.
Amaroo Orchards, Paringa SA
Food Processors
Clock IT! – Developed a Time and Attendance system that uses electronic Clocks placed in many locations throughout the property. The clocks capture employee movements and job numbers (cost centres) using swipe cards. The information in the clocks is then downloaded via either a network, phone modem or wireless link to the host Time and Attendance system. The host system calculates time allocations (e.g. Normal Pay, Overtime, RDO, etc) based on structured rules against Pay Classes (awards) for a pay week. This system also enables the payroll officer to make additional time allocations (e.g. Sick / Annual Leave, etc) and export the infor-mation to be used by a Payroll System.
Pay Rates are also captured in this system and along with the Job Number (cost centre) information collected at the clocks and subsequently downloaded to the host system and is also used to prepare cost allocation reporting. Many screens and reports are on offer to enable reconciliation with payroll and assist with labour re-source management.